HDPF FOAM CHINA FACTORY VISIT BY DRACON INTERNATIONAL
- Timikara Taurerewa
- Nov 12, 2024
- 6 min read
Updated: Jan 29
Timikara the director takes his cousin Ray Leef on a learning curve in the Chinese supply chain, lets skip the Canton Fair.
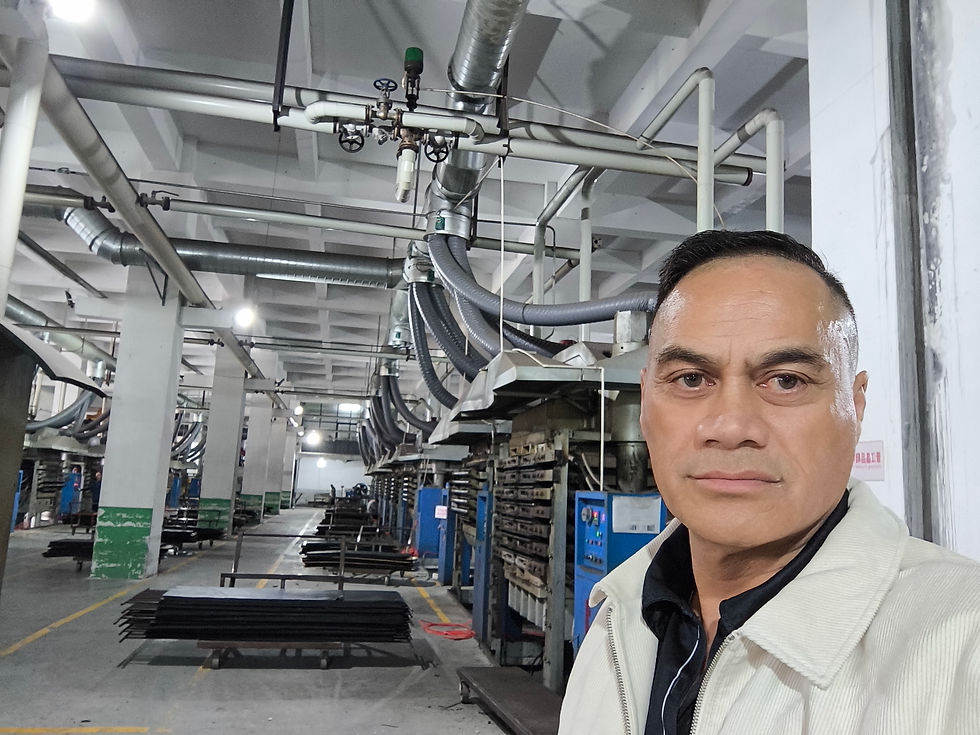
As the morning sun rose over the industrial hub of Quangzhou, China, Timikara, the director of Dracon International, with Ray Leef relation and master builder from Australia. They arrived at a bustling airport to be greeted by little sweet lady Mrs Zoe, her factory specializing in the production of HDPF Foam. Known for his hands-on approach and commitment to quality, Timikara was here to ensure the foam met Dracon International's high standards for durability, resilience, and sustainability.
The factory manager, Mrs Zoe, greeted Timikara warmly, leading him through the gates and into the first stage of the production line.
Stage 1: Raw Material Selection and Preparation
Timikara’s first stop was the raw material storage area, where large drums of high-quality polyethylene resin were stacked, ready for processing. Mr. Zhang explained the selection criteria, emphasizing that only the finest, sustainably sourced resins were used to maintain product integrity. Timikara examined the resin samples, appreciating the factory's dedication to eco-friendly practices and high-grade materials.
"These materials are the foundation," Timikara noted, "and it’s clear why your foam stands up so well in challenging environments."
Stage 2: Foam Extrusion
Next, they moved to the extrusion line, the heart of HDPF Foam production. Here, the resin was melted down and forced through a specialized die to create the dense, closed-cell foam structure. Timikara observed the high-precision machines at work, carefully controlling the foam’s thickness and density as it was shaped.
"This process is key to the foam’s durability," Mr. Zhang explained, pointing to a large screen monitoring each aspect of the extrusion. "Any variation, even minor, affects its resilience."
Timikara nodded, impressed by the factory’s meticulous control over each extrusion parameter. The foam was emerging just as he’d hoped – dense, consistent, and ready to take on the world’s harshest environments.
Stage 3: Quality Control and Testing
They proceeded to the quality control lab, where technicians in white coats were testing a batch of foam to ensure it met stringent specifications. Timikara watched as samples underwent compression testing, density measurement, and water resistance trials. One technician even submerged a piece of foam in water, watching to see if it would absorb any moisture—a critical test for Dracon's demanding applications.
Mr. Zhang held out a foam sample with a smooth, even surface. "Each piece undergoes this process to guarantee it meets your standards."
Timikara scrutinized the sample and smiled. "This is exactly the kind of quality we need. It’s obvious why clients trust HDPF Foam in high-impact applications."
Stage 4: Packaging and Logistics
In the final stage, Timikara observed workers packaging the foam for shipment. Each sheet was carefully wrapped and labeled, ensuring it would arrive safely at its destination without any damage. Mr. Zhang explained that packaging is tailored to each client’s specifications, minimizing waste and facilitating smoother transportation.
"Logistics is a crucial part of the supply chain," Mrs Zoe said, nodding to Timikara. "We understand the importance of on-time delivery, especially with Dracon’s global reach."
Timikara appreciated this attention to detail. His clients valued not only the product's quality but also its reliable delivery. Observing the foam prepared for shipment, he felt confident that his customers would receive their orders in perfect condition.
Final Thoughts
As they completed the tour, Timikara reflected on the rigorous process he had witnessed. From raw material selection to final packaging, every step was handled with precision, care, and sustainability in mind. HDPF Foam wasn’t just a product; it was the result of a deeply considered and meticulously executed process.
Standing with Mrs Zoe, and Ray Leef, Timikara extended his hand. "Thank you for giving me a closer look at what goes into HDPF Foam. It’s clear that your team is committed to the same values we hold at Dracon – quality, reliability, and a vision for a more sustainable future."
As he left the factory, Timikara felt a renewed confidence in the product he would soon be sharing with his clients around the world. He knew that HDPF Foam would not only meet but exceed the expectations of industries that needed a high-performance, eco-friendly matting solution. For Timikara and Dracon International, this partnership represented the best of global collaboration, bringing together innovation and integrity in every single sheet of HDPF Foam.
HDPF Foam: Leading the Way in Heavy-Duty Matting Systems with Innovative Technology
HDPF Foam has established itself as a trusted name in the heavy-duty matting systems industry, providing solutions that excel in durability, reliability, and adaptability across various challenging environments. Engineered with advanced closed-cell technology, HDPF Foam is designed to resist water, humidity, detergents, diluted acids, alkalis, alcohols, esters, and fungi, ensuring optimal performance even in the most demanding applications.
Unmatched Performance with Airtight and Resilient Properties
One of HDPF Foam's key advantages lies in its profile, which delivers an airtight finish, crucial for preventing air condensation, especially in cold-line applications. The foam's high-density structure absorbs the movement caused by pipe contraction and expansion, effectively preventing gaps or erosion around fittings over time. This resilience ensures a consistent performance that lasts throughout the life of the installation, making HDPF Foam a reliable choice for heavy-duty environments.
Manufacturing Excellence: Quality at Every Step
The production of HDPF Foam involves a rigorous process to ensure quality and consistency in every product:
1. Raw Material Selection and Preparation: High-quality polyethylene resin is sourced and prepared to ensure the integrity of the foam.
2. Foam Extrusion: The resin is melted and extruded to create a high-density foam with a uniform cell structure.
3. Quality Control and Testing: Each batch undergoes stringent testing to verify it meets the specifications for density, thickness, thermal conductivity, and water resistance.
4. Packaging and Logistics: Careful packaging and transportation logistics are arranged to protect the foam and ensure smooth delivery.
Close collaboration with clients and suppliers ensures HDPF Foam meets unique project requirements, handles seasonal demands, and provides timely delivery, making it a trusted choice for businesses needing high-performance matting solutions.
Verified Quality for International Standards
To maintain a high standard of quality, HDPF Foam undergoes a third-party inspection process, especially for international clients. This inspection verifies key quality metrics, including:
· Visual Inspection: Checking for surface uniformity and absence of defects.
· Dimensional Accuracy: Ensuring precise thickness and dimensions.
· Hardness Testing: Assessing the foam's durability and resilience.
· Compression Testing: Evaluating the foam's ability to withstand pressure.
· Thermal Conductivity Testing (Optional): Confirming insulation properties.
· Density Testing: Ensuring consistent weight per unit volume.
· Moisture Resistance Testing: Verifying the foam’s resistance to water absorption.
· Flexibility Testing: Confirming the foam's flexibility and endurance.
This inspection process ensures HDPF Foam products meet client-specific standards and are ready to excel in demanding environments, such as construction sites or high-traffic industrial areas.
Environmentally Conscious Manufacturing for a Sustainable Future
HDPF Foam is committed to environmental sustainability. The foam is crafted using sustainably sourced materials, and the production process prioritizes reduced environmental impact, aligning HDPF Foam with eco-conscious values. This responsible approach makes it an ideal choice for businesses aiming to reduce their environmental footprint while maintaining the highest standards of durability and reliability.
Versatility and Customization for Diverse Applications
HDPF Foam offers matting solutions in various thicknesses and densities, tailored to meet different operational needs. From high-traffic areas requiring cushioning to static-dissipative mats for sensitive equipment zones, HDPF Foam provides options that integrate seamlessly with each workspace's demands. Clients can select the right specifications for their environment, ensuring an ideal balance of support, resilience, and protection.
A Customer-Centric Approach
From consultation through installation, HDPF Foam’s dedicated customer support team ensures each matting solution aligns perfectly with specific requirements. This commitment to customer satisfaction has built a loyal following of clients who trust the brand for its product quality and dedication to sustainable practices.
Choose HDPF Foam for Superior Heavy-Duty Matting Solutions
For industries that demand high-quality, sustainable matting solutions, HDPF Foam stands out as a top choice, delivering products that combine durability, eco-consciousness, and reliable performance across a range of applications. Whether for construction, manufacturing, logistics, or other high-impact settings, HDPF Foam provides a trusted solution in heavy-duty matting systems.
Seeking a robust China supply chain or a dedicated China procurement arm for your business?
Elevate your business profits and enhance your return on investment. Reach out to Dracon International for a discussion about your project. We're here to share our experience with no obligations and no strings attached.
Connect to our company and our platforms, see below:
Signup newsletter: https://www.dracon.co.nz/
Our Case Studies: https://www.dracon.co.nz/case-studies
Instagram: https://www.instagram.com/timikara_dracon/
Face Book: https://www.facebook.com/DraconNZ/
#chinasource #sourcechina #chinaconstruction #buyChina #chinaprocurement #chinaagent #ChinaInspections #chinabuildingmaterials #chinaconstruction #chinarawmaterials #FactoryInspections #ChinaBuyingAgent #ChinaProcurement #SourcingInChina #ChinaConstructionMaterials #ChinaBuildingMaterials #ChineseSuppliers #GlobalSourcing #QualityControlChina #ImportFromChina
Comments